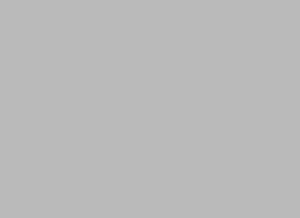
Recovery Section
The recovery section is designed to recover cooking chemicals from the black liquor received from the Brown Stock Washing section. Although this section is cost-intensive, it is necessary to minimize the use of fresh cooking chemicals, reducing the requirement to only 8-12% due to losses in the Brown Stock Washing process.
Main Components of the Recovery Plant
- Multiple Effect Evaporators
- Low-Temperature Incinerator
- Recausticizing Plant
Multiple Effect Evaporator Section:
The black liquor received from the Brown Stock Washing section has a concentration of 0.8-1.5%, depending on the raw material used. The concentration of the black liquor is increased to 25-30% in the evaporator section. Different types of evaporators, such as Long Tube Vertical Evaporators, Falling Film Evaporators, and Natural Circulation Evaporators, are used based on the quality of the black liquor.
Falling Film Evaporators are commonly used in the paper industry due to their advantages over Long Tube Vertical Evaporators. In a Falling Film Evaporator, the black liquor is pumped from the vapor head to the distribution plates above the tubes, allowing the liquor to fall within the tubes. These evaporators operate at a low temperature difference, allowing multiple effects to be installed in series and offering better steam economy.
Low-Temperature Incinerator (LTI):
The LTI uses a fluidized bed technique to treat black liquor from the Multiple Effect Evaporator, recovering pulping chemicals and reducing environmental pollution. The LTI is suitable for paper mills processing less than 300 tons of black liquor solids per day.
Advantages of LTI include:
- Elimination of air and water pollution.
- Removal of BOD and color from residual organic products.
- Removal of particulate matter and gases before discharge into the atmosphere.
System Components:
- Low-Temperature Incinerator with accessories
- Venturi Scrubber System with Cyclone Separator
- Attrition Mill and other accessories
- Air Pre-heater with HSD Burner
The semi-concentrated black liquor from the evaporator is fed to the Venturi Scrubber, which operates as a direct contact evaporator, increasing the black liquor concentration to 45%. This black liquor is then fed to the LTI, where temperatures are maintained around 600-700°C, evaporating the water and converting solids to soda ash. The soda ash is withdrawn from the reactor using a variable speed rotary valve and conveyed through a water-cooled screw conveyor before being stored in a silo.
Recausticizing Plant:
The soda ash (Na2CO3) produced in the LTI is treated with milk of lime (Ca(OH)2) to produce caustic soda (NaOH), which is used in the digester for cooking raw material. The calcium carbonate (CaCO3) produced can be used as landfill or sold to the cement industry.
Major Equipment:
Lime Slurry Preparation
- Table Feeder: Feeds lime to the slaker at a controlled rate.
- Rotary Drum Slaker: Adds water to lime to make slurry, rotating at a fixed speed to complete the reaction. Grits are removed from the slaker.
Classifier: Mixes green liquor from the LTI with lime slurry, removing any grits in the system.
Causticizer: Pumps slurry from the rake classifier to the causticizer, installed in series to provide retention time for the reaction. It includes an agitator and is sized according to capacity.
White Liquor Clarifier: Pumps slurry from the causticizer to the clarifier, which has a rake mechanism to ring sludge to the center. The overflow is taken to a storage tank for use as cooking chemicals in the digester house.
Recausticizers: Mixes underflow from the white liquor clarifier with washed liquor from the first-stage lime mud washer.
Lime Mud Washer: Similar to the white liquor clarifier, provided in series to recover chemicals from lime sludge using a counter-current system.
Lime Mud Filter: Works on vacuum to filter sludge from the final lime mud washer. The inlet consistency is around 1-1.5%, and the outlet consistency is around 60%. The filtered lime sludge can be used in landfills or sold. The lime mud filter includes a filtrate tank.